Page 2: 3D vision-guided robot automates harvesting of chicken fillets
Editor's note: Continued from page one.
"Machine vision makes the entire procedure adaptive as it allows us to localize the gripping point of the fillet independently of the variations in size," said Misimi.
The most challenging aspect in this research was the development of the gripper, which had 3D printed plates, due to the variations in mechanical properties and texture of the chicken. More research is needed to understand the complete scope of the effects of the texture and mechanical variations of the fillet texture on the gripping operation. However, the Gribbot concept proved to be successful, suggested Misimi.
"The Gribbot shows that there is huge potential for the robot-based automation for handling, processing, and sustainable use of raw materials. The aim of our research was to develop a flexible and adaptive robot-based concept that is able to handle and process raw materials with different material properties and high biological variations," he said.
In addition, the system was designed to enable a sustainable market-tailored production according to customer demands. The hygienic design of the gripper plates is something that will need to be focused on the future, particularly if a vendor is interested in the concept, but as this is a research-based project and not a commercial product, this is something that is yet to be determined.
View more information on SINTEF.
Share your vision-related news by contacting James Carroll, Senior Web Editor, Vision Systems Design
To receive news like this in your inbox, click here.
Page 1 | Page 2
About the Author
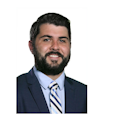
James Carroll
Former VSD Editor James Carroll joined the team 2013. Carroll covered machine vision and imaging from numerous angles, including application stories, industry news, market updates, and new products. In addition to writing and editing articles, Carroll managed the Innovators Awards program and webcasts.