3D Imaging: Time-of-flight (TOF) camera measures box volume
Effective use of space is one key to optimizing operational efficiencies in many industries and applications. Packing parcels for shipment is a case in point. As items are placed in corrugated boxes or shipping containers, fill material such as packing peanuts, molded pulp chips or other things are added to minimize void space and protect items from damage during transport.
The goal is to use just the right amount of packing material. Too little and the risk of objects in the parcel shifting and becoming damaged during transport increases. Too much packing material wastes resources, which can quickly add up for organizations shipping a large number of parcels on a regular basis. Plus, manual operation of the fill-material dispenser can be labor intensive and prone to errors.
To help the profitability of their customers, one German packaging OEM that makes production equipment for filling machines, was faced with the task of automating the fill material dispensing process. In turn, the machine builder tapped Eye Vision Technology (EVT; Karlsruhe, Germany;www.evt-web.com) to develop a vision system to perform the task of real-time, box-volume, measurement.
To that end, EVT has developed the 3D EyeVolume measurement system that incorporates a TOF sensor from Bluetechnix (Wien, Austria;www.bluetechnix.at) and a new user interfaced based on EVT EyeVision image processing software.
"Time-of-flight sensor technology is a good fit for this application for three main reasons," explains Michael Beising, CEO of EVT. "It's more cost-effective than other 3D scanning technologies such as fringe pattern projection and 3D laser displacement sensors. It doesn't require a motion axis for scanning the box as would a 3D laser displacement sensor. And, it runs at up to 40 frames per second, providing real-time volume measurements as the box is being filled with packing material."
3D TOF cameras illuminate the object to be imaged using a light source that is either pulsed or modulated by a continuous wave source. In the pulsed mode approach, the measuring of short time intervals between the emitted and reflected light are used to compute depth information. In continuous wave systems, the phase shift between the light source and the reflected light is measured and the distance to the object would then be computed.
For this application, the EVT design team decided to trade off higher costs and higher resolution for faster, and lower-priced technology. "While the TOF sensor doesn't offer as high of a resolution as competitive 3D technologies," says Beising. "It does offer the speed needed for this real-time box volume measurment application, and the resolution is sufficient enough to determine box volume within one cubic centimeter, which is all that's required."
During configuration, the first step in the process, the operator closes the box and places it under the scanner. The scanner measures the height of the box and probes the edges to determine its position, then measures the interior volume of the box.
"First each container has to be configured in this way ," Beising explains. "But once configured in the system, boxes are automatically recognized by the host computer."
During operation, the box-volume measurement system is able to detect the container, regardless of orientation, so the box does not have to be fixed in its position.
As the box is being filled with items or packing material, the program continuously measures the remaining volume in the box and communicates real-time results via RS232, Ethernet or Profinet to the machine controller or host computer. When the box is full with just the right amount of packing material, it signals the machine to turn off the fill material dispenser.
In addition to reducing labor costs and material waste to improve profitability, Beising notes, the system also minimizes the risk of damage to products and brand reputation, and decreases the number of costly returns.
About the Author
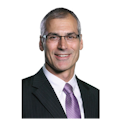
John Lewis
John Lewis is a former editor in chief at Vision Systems Design. He has technical, industry, and journalistic qualifications, with more than 13 years of progressive content development experience working at Cognex Corporation. Prior to Cognex, where his articles on machine vision were published in dozens of trade journals, Lewis was a technical editor for Design News, the world's leading engineering magazine, covering automation, machine vision, and other engineering topics since 1996. He currently is an account executive at Tech B2B Marketing (Jacksonville, FL, USA).
B.Sc., University of Massachusetts, Lowell