The makings of a successful imaging lens: Part one
Part one: Application and specification development
Greg Hollows
Imaging and vision is all around us - it solves problems and enhances our lives on a daily basis. The pace of its advancement shows no signs of slowing. The future is filled with autonomous vehicles, more sophisticated automation in factories, collaborative and service robots, advanced medical diagnostics for improving lives, and numerous forms of personal entertainment, all of which are powered by vision.
These developments are heavily reliant on advancements in sensor technology, image processing, and imaging sciences. However, this dependence creates extreme pressure and bottlenecks on other technologies within these systems.
Optical technology is experiencing more pressure than ever to create the solutions necessary to meet an increasingly diverse set of markets, all with varying demands and expectations. Developing the needed products is a multistep endeavor requiring different skills and areas of expertise. This three-part article series will review the different stages of developing an imaging lens, outline what is required for success, and identify how to mitigate undesired outcomes.
Future articles in this series will delve into optical fabrication, the effect of tolerances, material costs, testing, metrology, and performance validation. In part one, we begin with specification development and design considerations.
First, the application
Regardless of the required development speed, developing a robust specification early on will reduce headaches, cost, and schedule delays. Experienced optical designers will ask many questions at the start of a design project, some of which may not feel completely related to the design request. In trying to prioritize multiple competing specifications, seasoned optical designers want to know as much as possible about the application in order to achieve the end goal in the most reliable, cost-efficient way.
Lack of information usually leads to over-specification. Inevitably, a few things happen in this situation: the design cycle takes longer than required, costs are usually higher, and in some cases, a solution is never obtained. Being as open as possible about the application at the onset of a project will only help to avoid unforeseen, undesirable, and unexpected outcomes.
While there are a number of applications utilizing off-the-shelf designs, many modern applications necessitate designs that do not exist today. Most designs require some level of tradeoff between multiple specifications, and several of these new designs stretch the limits of what can be created. One cause of this is that many specifications compete with each other, both in the design process and fabrication.
Additionally, many specifications are intertwined; changing one specification usually affects at least one other specification. While the directionality of changes made are usually known, the magnitude of their effect cannot be fully determined until some design iterations are completed. Finally, various aspects of a specification can have far-reaching or long-lasting effects on both the design and fabrication process. Understanding requirements such as cost, size, and weight helps understand how they may create other limitations further on in the development process (Figure 1).
Figure 1:This Dilbert comic illustrates how robust specification development is important at the onset of a project. Specification changes can sometimes have hidden costs (DILBERT © 2004 Scott Adams. Used By permission of ANDREWS MCMEEL SYNDICATION. All rights reserved).
Cost drives choices
Cost is a very important part of the discussion and should be reviewed early on and anytime a modification to a specification is made during the development process. Cost is continually discussed when building out a specification as it drives decisions on the types of manufacturing equipment and materials used for making the desired imaging lens.
This will likely change how the design is developed, as well as its limitations. Cost can be viewed as a monolithic parameter: some costs in the process are more sensitive and risky than others. Is production pricing the main driving force? Are upfront engineering and NRE (non-recurring engineering) costs a driving concern, but product pricing a little less sensitive? Are multiple rounds of prototypes tolerable as an expense? Are multiple rounds of prototypes sufficient from a time-to-market (lost sales) perspective?
Example customer requirement: A customer requires creation of a new product with very good performance. Initial prototypes will be required, and afterwards will move to high volume production, with high cost sensitivity in production. After reviewing the basic needs of the customer’s system, there is a combination of technical specifications competing with each other and also extreme high-volume price sensitivity requirements. Utilizing specialized production equipment can overcome both of these issues, but this comes with significant tradeoffs.
Specialized high-volume production machines, like those used for glass molding, may have exceptionally high upfront costs for the molds and other NRE fees. If a small quantity is needed for proof-of-concept purposes, the cost could be overwhelming - especially if the concept is changed, as all the upfront costs will be incurred again. However, high volume production techniques such as glass molding offer the benefit of much lower long-term production costs. On the other hand, conventional grinding and polishing offers lower-cost solutions in the prototype phase, though usually struggle to meet the more cost-effective, high-volume requirements.
In the design process, molded lenses offer additional degrees of freedom that conventional fabrication cannot. Essentially, molding allows for creating shapes that conventional grinding and polishing equipment cannot make (Figure 2). When an optical designer is given the option to use molding compared to conventional fabrication, the result is a very different optical design. Shifting a design from one manufacturing technique to another is not trivial and creates significant delays in the overall development process as the design may have to begin again from scratch. Molding also requires for the selection of very specific glass types, which may also be a limitation to thedesign.
Figure 2:Molding allows for the creation of lens geometries that are impossible to achieve using conventional grinding and polishing such as this gullwing aspheric lens (left). Conventional lens manufacturing is often limited to less complicated geometries like this aspheric lens with no inflection points (right).
Another cost consideration is the glass materials used for the design, regardless of the fabrication process. There are hundreds of different glass types to choose from that cover a wide cost structure and have varying yield rates when machined in lens-element production. Allowing an optical design to use any glass type will increase the likelihood of designing a fully compliant technical solution but will also lead the way to higher cost solutions.
Beyond performance-based specifications such as resolution, physical requirements like size and weight will also significantly drive glass choice and affect cost. In order to reduce size and weight, the number of glass elements is typically reduced. Reducing the number elements reduces the degrees of freedom in a design, thereby requiring more flexibility with glass section and lead to higher glass costs, thus creating higher cost solutions.
Size and weight
Many new machine vision and image processing applications are approaching the limits of the laws of physics for lens designs when they relate to specifications such as resolution and depth of field. While flexibility on all specifications is beneficial, hitting the aforementioned specifications can be very difficult if a lens design does not have the flexibility to grow to the size required (Figure 3). Allowing size flexibility typically leads to better performance, less sensitivity in fabrication, and may even lead to lower costs if avoiding higher priced glasses. For a number of reasons, it is not always practical to allow a lens design full size and weight freedom. However, keeping this as a consideration during early specification development allows for more freedom and flexibility during the lens design phase.
Figure 3:Many applications require large imaging systems to achieve their desired performance. Allow ample room for the imaging system to avoid having to make sacrifices to system performance.
Remember to be flexible and open when discussing an application and design specifications. Potential obstacles with cost, schedule, size, weight, and other requirements can be avoided if proper information is provided from the onset. Understanding specification development and design considerations are critical to creating a successful outcome. Part two of this series will look at understanding performance-based specifications and their design considerations.
Greg Hollows,Vice President, Imaging Business Unit, Edmund Optics
(Barrington, NJ, USA; www.edmundoptics.com)
About the Author
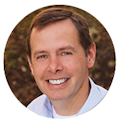
Gregory Hollows
Gregory Hollows is the Vice President of the Imaging Business Unit in Edmund Optics’ Barrington, NJ, USA office. He is responsible for everything pertaining to vision and imaging for EO, including the business plan, strategy, and product marketing. He is also responsible for the overall growth in imaging optics sales.
He enjoys having the opportunity to affect what imaging products EO puts forth, while helping customers solve problems. The personal gratifications that come with knowing that EO imaging products are helping in many different fields and applications make all of his effort and hard work worthwhile. Gregory previously held positions as Engineering Technician and Engineering Manager. He received Bachelor degrees in Physics and Chemistry from Rutgers University located in New Brunswick, New Jersey.