3D scanners and printers enable rapid reusable N95 mask production
Shortages of personal protection equipment (PPE) for healthcare facilities in the United States put front line workers treating COVID-19 patients in danger of contracting the virus. Seeking a quick and effective way to help remedy the situation, a collaborative team of researchers from the University of Kentucky (Lexington, KY, USA; www.uky.edu) and Seikowave (Lexington, KY, USA; www.seikowave.com) have developed a manufacturing process, using 3D scanners and printers, with the potential to fabricate thousands of custom-fit, reusable respirators for healthcare workers in a single day.
Matt Bellis, CEO from Seikowave, collaborated with Dr. Daniel Lau, Professor of Electrical and Computer Engineering at the University of Kentucky and Vision Systems Design Editorial Advisory Board member, and Dr. Michael Winkler, a radiologist at the University of Kentucky's Gill Heart and Vascular Institute. Winkler first learned about the high-speed 3D imaging capability developed by Lau through one of the many programs at UK that foster internal collaboration. Curious about the capabilities of 3D scanning a face for purposes of creating custom-fit respirators, Winkler contacted Lau about the urgent need to provide appropriate protection for medical workers.
Related: Understanding the latest in high-speed 3D imaging: Part one
When asked about the importance of fabricating custom-fit respirators, Lau replied:
“Because doing so provides a custom fit, 3D scanning a person’s face gives them a much better feel when wearing the mask than wearing a generic-sized mask, which are in short supply anyway,” says Lau. “Everyone has seen the images of people wearing masks for long periods of time with bruises. A customized mask alleviates this issue.”
Instead of scanning faces with campus equipment, Lau suggested walking over to 3D imaging company Seikowave—a company Lau co-founded—where the team was already working on a 3D face scanning system for dental applications and thus better equipped for such an undertaking. After tweaking the software parameters based on scanning a whole head instead of a tooth, the team quickly scanned Lau’s face and sent it to Siavash Tohidi, School of Art and Visual Studies (SAVS) faculty member, for printing on a FormLabs (Somerville, MA, USA; www.formlabs.com) 3D printer (Figure 1).
In the setup, four Seikowave 3DSL Rhino cameras capture images of a person. This structured light 3D camera features the CMV300 VGA CMOS image sensor from ams (Premstaetten, Austria; www.amso.com) and captures images in this application at up to 700 fps. The speed of acquisition ensures that inaccuracies from subject are well within the custom-fit respirator (CFR) design tolerances. After acquisition, Seikowave software renders a 3D model and converts the data into a CAD surface for use in Creo Parametric 3D modeling software from PTC (Boston, MA, USA; www.ptc.com). Seikowave engineering manager Shawn Thomas developed a base design that could be easily modified (Figure 2). The operator adapts the Seikowave design to the contours of a person’s face using features in CREO that allow for rapid alignment of shapes. The process takes about 15 minutes in total.
Related: 3D-vision-guided robots assist in COVID-19 measures in China
Once the custom fabrication component prints (Figure 3), it pairs with the three-piece, injection molded filter holder, filtration media is added into the mask, and it gets assembled and tested. Currently, the University of Kentucky has an effort underway for testing different filtration medias to determine which ones will meet N95 requirements and feedback is expected soon.
“Preliminary feedback shows some promising candidates, and the team expects to narrow the group of candidates down to just a few by as early as next week,” says Bellis. “After this, we should be ready to go into full fit test verification.”
Acquiring 3D scans of the face using the 3DSL Rhino is straightforward. However, the team did not have the engineering resources to create a mobile scanning station. After taking part in a call with business leaders from the state of Kentucky on COVID-19 relief, however, Seikowave CEO Matt Bellis found help from the local Toyota manufacturing facility (Georgetown, KY, USA; www.toyotageorgetown.com).
“After describing the system on the call, the GM of the Toyota plant offered access to engineering and fabrication resources,” says Bellis. “The group basically took the initial configuration of scanners on tripods and created a robust frame. Now they are taking the next step by building the frame into a mobile scanning station that will travel to various hospitals in the area.”
While safety remains the main driver behind the idea, the CFR’s physical fit must be considered as well. Nobody wants to wear an uncomfortable respirator for hours on end. To that end, the team opted to use EnvisionTEC (Dearborn, MI, USA; www.envisiontec.com) 3D printers, which use a bio-compatible material that fits nicely against a person’s face. Initially developed for medical/dental applications, a proprietary resin material developed by the company suits respirator needs, according to Bellis, who says the custom-fit respirators have the right chemical characteristics and material proprietary needed for a good interface with the skin.
Furthermore, once the team have emergency use authorization in place for the design, they will have access to approximately 100 EnvisionTEC 3D printers, allowing the project to scale quickly, says Bellis.
“One hundred of these printers would allow the scanning and printing of thousands of respirators per day,” he says. “As soon as June these respirators could be going to frontline workers or businesses in need of PPE.”
He adds, “Because these are reusable respirators and will be custom fit to an individual, this represents an ideal solution to start getting these out to places that want to reopen.”
Seikowave is building systems to ensure that there are 3DSL Rhino scanners to meet the need for scanning people. Seikowave has been contacted by many customers willing to temporarily contribute their scanners to this effort. By late May, the potential exists to have as many as 40 different scanning centers operational, enabling the acquisition of 3D data on thousands of people per day, explains Bellis.
Related: Thermal imaging: Learn the limits of elevated body temperature screening
While currently a manual operation, the matching of 3D scans of a face to a custom-fitting respirator is something the Seikowave team is addressing.
“The ultimate goal is moving to scan-to-print, without the need for manual modifications,” says Bellis. “Once the design is locked in, it is possible to move to a completely automated, software-driven solution, and the team is working toward this goal.”
Phase one of the project involves people coming to scanning centers or the Seikowave team driving to a large facility like a hospital where the 3D scanning system captures images of hundreds or thousands of faces. Should this approach be implemented and prove successful, the team has a phase two approach planned that involves getting respirators created even more rapidly.
About the Author
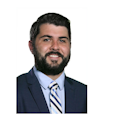
James Carroll
Former VSD Editor James Carroll joined the team 2013. Carroll covered machine vision and imaging from numerous angles, including application stories, industry news, market updates, and new products. In addition to writing and editing articles, Carroll managed the Innovators Awards program and webcasts.