Automated inspection system detects errors in hard disk drive production
Perfectly fitting and sealing a hard disk drive’s (HDD) magnetic disks into their cases ensures proper functioning of the device as well as protection against dust, humidity, shock, and vibration. With little room for error in the production of an HDD, using machine vision systems for precise inspection and quality control makes economic sense.
System integration company Flexon Technology (Pathum Thani, Thailand; www.flexontechnology.co.th) specializes in vision inspection systems, automatic-optical inspection modules, and automatic machines and software for data management. Supported by Dynatech Instrument (Samsennok Huaykwang, Bangkok, Thailand: www.dynatech.co.th), a partner of Allied Vision (Stadtroda, Germany; www.alliedvision.com), Flexon Technology developed the Visual Inspection Machine (VMI) to detect errors in HDD production.
The VMI incorporates two cameras from Allied Vision. The Mako G-125B is a monochrome 1.2 MPixel camera with GigE interface and Power over Ethernet (PoE), equipped with a Sony ICX445 CCD progressive global shutter image sensor with 3.75 µm pixel size. The Manta G-505B is a monochrome 5 MPixel camera with GigE interface and PoE, equipped with a Sony ICX625 CCD progressive global shutter image sensor with 3.45 µm pixel size.
HDDs for inspection enter the VMI through a conveyor belt. At the first inspection station, a Mako G-125B inspects the top of the HDD case for missing or incomplete threads, thread damage, missing machining surface, and missing drill, inspecting 14 locations in total. A Manta G-505B takes an image of each of the 14 locations. The total time for inspection on station one is 4.2 seconds.
The HDD is then flipped over on its way from the first station to the second station. Four cameras are located at the second inspection station, three Mako 125-Bs and one Manta G-505B. Two of the Mako cameras each scan one side of the HDD case for missing or incomplete thread. The third camera inspects the back of the case for missing or incomplete thread as well as missing riveting, missing drill, machining surface, and also reads the part numbers.
The three Mako cameras capture 14 images between them, in total. The Manta camera locates the position of the thread hole. Inspection time at station two is 4.8 seconds. At this point the HDD case is either moved to the load out conveyor if it passes inspection or moved to the reject pile if errors were detected.
About the Author
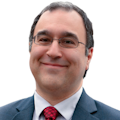
Dennis Scimeca
Dennis Scimeca is a veteran technology journalist with expertise in interactive entertainment and virtual reality. At Vision Systems Design, Dennis covered machine vision and image processing with an eye toward leading-edge technologies and practical applications for making a better world. Currently, he is the senior editor for technology at IndustryWeek, a partner publication to Vision Systems Design.