Lighting controllers for machine vision applications
Andrew Wilson, Editor
Increasing the contrast of image features often results in reduced image processing software overhead and thus increased system performance. To do so requires an understanding of the product being inspected and the type of lighting required to achieve this task. In many machine vision systems, LED lighting has replaced fluorescent and quartz halogen lighting due to the increased intensity of LED products, their stability, long lifetimes and cost-effectiveness. Today, numerous vendors offer such lighting products in various configurations including spotlights, ring lights, backlights, dome lights and line-lights.
Configured with different wavelengths of LED illuminators, these lighting products are each designed to meet the needs of specific machine vision applications. Each one of these different configurations can increase the image contrast of captured images depending on the nature of the product to be inspected (see "Lighting design enables vision systems," Vision Systems Design, December 2005; http://bit.ly/IqkPQO and "Choosing illumination for vision systems," Vision Systems Design, February 2004; http://bit.ly/1bGcjcT).
Constant current
While the choice of the type of LED illuminator and wavelength is important so is the choice of the lighting controller. Here again, the choice of a lighting controller is application dependent. In some applications, such as line-scan inspection systems, for example, it is necessary to continuously illuminate the product being inspected. In other applications, where an area array camera must capture images of objects at high-speed, the LED illuminator may need to be strobed.
In other applications, it may be necessary to illuminate objects with multiple LED lights or with varying illumination intensity to extract the relevant features from the object being imaged. In such cases, intelligent lighting controllers that incorporate selectable intensity, pulse control, speed and programmable illumination sequencing can meet these demands.
For machine vision applications, lighting controllers that provide constant current sources are offered by most LED lighting and controller manufacturers since LED brightness is determined by the current flowing through the LED not through the voltage. While voltage controllers are available, they are not recommended for machine vision applications since small voltage changes result in large current changes and hence a large change light intensity. However, by regulating the current through the LED, constant current sources ensure that the absolute maximum rating of the LED being driven is not violated and a predictable and stable luminous intensity is obtained.
Integrated controllers
"Many machine vision LED manufacturers require the use, and purchase, of their own LED driver or an aftermarket driver/controller. Over the years, users have become familiar and comfortable with the idea of using these external devices to power and control LED illumination systems. With advances in LED driver technology, however, microprocessor controlled micro-drivers can be designed and integrated into the light, effectively eliminating the need for an external controller," says Casey Segraves, Business Development & Marketing Manager of Smart Vision Lights (Muskegon, MI; http://smartvisionlights.com). Microprocessor-based, the company's SMART driver integrated into its range of LED lighting products allows continuous illumination to be controlled through a 0-10V DC signal or strobed operation to be controlled using a pulsed input.
With applications that require continuous illumination, the intensity is the only parameter that needs to be set. In such applications, it may only be necessary to use an LED intensity controller to adjust the amount of light from the LED. If intelligent lighting products such as those from Smart Vision Lights are not specified, then it is necessary to specify an external LED lighting intensity controller. Units such as the CS420 from Advanced illumination (Rochester, VT; www.advancedillumination.com), for example, are dual output devices that can be controlled over a serial interface to perform this task (Figure 1).
"While built-in controllers may give a cost saving in some cases, the cost saving in having the stable light control that an external controller can provide pays back many times due to the higher reliability and repeatability of a machine vision system. The cost argument wears thinner still in systems with more than one light, where the additional cost of the built in controller has to be paid twice, compared to a single two channel external controller," says Peter Bhagat, Managing Director of Gardasoft Ltd (Swavesey, Cambridge, England; www.gardasoft.com).
"With an external controller multiple lights can be synchronized to work together, rather than all working individually. In systems where a single position is used to take multiple images of a product, the lights can be sequenced to turn on at different times or with different intensities so that multiple images can be taken in different lighting arrangements," Bhagat adds.
Both external controllers such as the ULC-2 controllers and LED controllers embedded in the lights are offered by Metaphase Technologies (Bristol, PA, USA; www.metaphase-tech.com). "OEMs will sometimes use the external ULC-2 to determine required light parameters such as intensity, max strobe rate and pulse width and then purchase the lights with embedded controllers with these values fixed for the final systems. This saves space and cost in the final OEM product," says Mark Kolvites, Technical Sales Manager at Metaphase Technologies.
High-speed applications
In high-speed applications that require strobed illumination, the lighting is switched on for a fixed amount of time when required and must be synchronized with the exposure time of the camera. In such applications, the controller receives a trigger signal when the camera exposure is about to start.
"If the product can be imaged without stopping its motion, the system will work faster and be subject to less mechanical stress. To do this requires a fast strobe pulse to freeze motion and precision overdriving to provide the extra light needed for a short exposure time. Particle velocity applications also require high brightness for a very short time period, sometimes less than one microsecond," says Peter Bhagat, Managing Director of Gardasoft.
To meet the needs of multiple applications, the delay from the trigger to the output pulse, the length of the pulse and the intensity and duty cycle of the pulses need to be configurable. Such strobe lighting results in a number of benefits, namely allowing increased brightness to be obtained from the LED illuminator while at the same time increasing its lifetime. In many machine vision applications, multiple lighting configurations may require intensity control and high-speed synchronization from single or multiple triggers.
To accomplish this, controllers with multiple trigger inputs and current output channels can be employed. Controllers such as Metaphase Technologies' Universal LED controller, for example, provide independent constant-current control of two LED illuminators with output currents ranging from 0.1 to 40 A when used in strobed mode (Figure 2). To allow external triggering, each channel has its own separate trigger inputs.
In some applications, it may be necessary to allow an individual trigger to control the output of multiple LED illuminators or use multiple triggers with multiple output channels. To meet these demands, products such as the RTCC4 Combined LED Control and Trigger controller from Gardasoft feature four opto-isolated trigger inputs and four independent current outputs. Each channel can be individually configured to output continuously or in pulsed mode based on an external trigger signal or internal timer. Furthermore, any individual trigger can control any output channel or group of output channels. Because the unit also features an additional two digital outputs, the unit can also be used for triggering external cameras and reject mechanisms.
Overdriven illumination
Machine vision applications where strobe lighting is used may often require high illumination. To achieve this, LED illuminators can be overdriven to increase the light intensity for a short duration. Often this increased light intensity will result in a higher contrast image being captured or allow the system to run faster.
At their specified current rating, LED lights will output 100% brightness. However, it is possible to obtain more than 100% brightness by driving with more current rating for short pulses. Most area scan systems can benefit from this overdriving but line scan systems normally cannot since continuous lighting is required. For applications requiring overdriving using a current driving lighting controller is critical.
To overdrive the LED light by a factor of two, for example, the current output must be doubled. Equally it is important to ensure that too high a duty cycle is not selected since this may damage the LED illuminator.
In its E-Series and X-Series product lines, for example, Spectrum Illumination (Montague, Michigan, USA; www.spectrumillumination.com) has developed a patented built-in controller that can be used to overdrive the light or drive the light in continuous mode (Figure 3). When the PNP or NPN strobe input is activated and held on, the output to the LEDs is set to the maximum "Instead of having to purchase a continuous run light or a strobe only light or special pulse controller we have found a way to accomplish both with a single product," says Dave Muyskens, President of Spectrum Illumination.
Remote control
While today's current controllers offer stable light output, high output currents, precision pulsing and overdriving, high-speed sequencing, they can also be used to perform remote configuration changes where it is necessary to remotely set and/or reconfigure lighting parameters for a particular application.
To accomplish this, many lighting controller vendors supply programmable controllers that can drive a variety of third party LED lighting products. The Compact 1 and 2 channel computer controlled LED drivers, for example, from Mightex Systems (Toronto, Ontario, Canada; www.mightexsystems.com) are supplied with a PC based software package with a GUI that enables the LEDs to be driven without the need to write code (Figure 4).
"As LED manufacturers continue to improve the intensity and the efficiency of their products, high speed applications that traditionally would use some other type of illumination technology will be replaced by LED lighting," concludes Kolvites. The associated benefits of longer lifetimes, strobe control and ease of programming will provide systems developers with low-cost means of high-intensity illumination.
Company info
Advanced illumination
Rochester, VT
www.advancedillumination.com
Gardasoft
Swavesey, Cambridge, England
www.gardasoft.com
Metaphase Technologies
Bristol, PA, USA
www.metaphase-tech.com
Mightex Systems
Toronto, Ontario, Canada
www.mightexsystems.com
Smart Vision Lights
Muskegon, MI
http://smartvisionlights.com
Spectrum Illumination
Montague, Michigan, USA
www.spectrumillumination.com
Vision Systems Articles Archives
About the Author
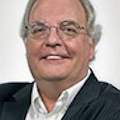
Andy Wilson
Founding Editor
Founding editor of Vision Systems Design. Industry authority and author of thousands of technical articles on image processing, machine vision, and computer science.
B.Sc., Warwick University
Tel: 603-891-9115
Fax: 603-891-9297