Quantum Dot Technology is Enabling Machine Vision Applications
Once thought of as a scientific curiosity, quantum dots (QDs) are revolutionizing multi-billion-dollar imaging and sensing markets worldwide.
Every year, more applications for these nanoscale semiconductors are coming to light. Well suited for everything from imaging to photovoltaics, QDs have contributed to an explosion of growth for the machine vision sector, with analysts predicting that the market for these materials could reach $360 million by 2027.
As rapid advances in artificial intelligence (AI) and camera systems fuel further demand for short-wave infrared (SWIR) sensitivity, QD technology is advancing at pace. Breakthroughs in synthesis methods and alternative formulations will bring QDs into an increasingly diverse range of sectors, and as the technology develops further, the next generation of SWIR sensors is becoming more accessible.
What are Quantum Dots?
QDs are nanoscale semiconducting materials that can respond to wavelengths up to 2,600 (nanometers) nm. Broadly speaking, they can be categorized as either colloidal or epitaxial. Whereas epitaxial QDs are produced using high energy ‘dry’ chemistry techniques, colloidal QDs are produced using benchtop ‘wet’ chemistry, granting them unmatched optoelectronic properties, as well as precise size control during the synthesis process. As a result, colloidal QDs are markedly cheaper and easier to produce than the epitaxial alternatives and are the variant most used in vision systems.
Colloidal QDs (hereafter simply ‘QDs’) typically measure between two and 10 nm, or just a few atoms wide. QDs for photodetection applications are made of a semiconductor core with an organic ligand shell that enables them to disperse in solvents. This facilitates the use of inexpensive deposition methods such as spin-coating, whereas epitaxial QDs require constraints such as a lattice match and thermal budget.
Most QDs are produced using long-chain organic ligand exchange, granting outstanding control over their growth and helping to retain their colloidal stability in solvents. During this process, long-chain organic ligands are replaced with shorter, more conductive ligands, which make the QDs more suitable for use in optoelectronic devices and increase electronic coupling between the nanoparticles in solid films.
The ability to produce QDs that are just a few atoms wide has the benefit of increasing their quantum confinement effect compared with wider epitaxially-produced alternatives.
When a particle is relatively small compared to the wavelengths of the electrons that it contains, the quantum confinement effect can be observed. QDs are essentially a small semiconductor box, and as this box reduces in size, the band gap between the valence state and conduction band is reduced. This increases the potential energy of the confined electrons, resulting in particles that exhibit extremely tunable emission wavelengths.
Infrared Imaging and Sensing
The ability to tune QDs to different wavelengths grants them a broad range of applications for new and emerging technologies. The bright, vibrant colors that can be produced using QDs, combined with the efficiency of this technology, makes them well suited to display applications, tapping into visible light wavelengths. QDs can be added to films, filters, glass, and electronics used in LCD displays to produce highly precise images, and as a result, this technology is already widely used in commercial televisions and computer monitors.
However, these applications of QD technology are just scratching the surface of what it is capable of. Truly reaping the benefits of QDs and ushering in a paradigm shift for the machine vision sector, requires materials that are tuned to wavelengths beyond the visible—the realm of infrared light.
Machine vision and imaging systems have benefitted from the advent of high-performance SWIR sensing technology. Indium-Gallium-Arsenide (InGaAs) sensors are already widely used, but the cost of InGaAs has so far limited its potential. InGaAs sensors often cost up to $10,000 per unit; a price that is inflated by the high rate of defects experienced during batch production.
Creating an InGaAs sensor requires the material to be epitaxially grown onto indium phosphide (InP) wafers and diced into chips. Pixels are then indium bonded with silicon readout circuits in a process known as ‘flip chip hybridization’ which, putting aside the high cost of production, results in limited pixel pitch and resolution. The inherent fragility of InP materials also makes it challenging to create wafers at larger sizes.
Some InGaAs sensors attempt to overcome their limited pixel pitch by instead using copper-copper (Cu-Cu) hybrid wafer bonding technology. However, these sensors are more susceptible to noise due to the high dark current they experience at room temperatures, meaning bulky cooling systems are needed to achieve the desired image quality.
In addition, sensors based on InGaAs technology are incapable of accessing wavelengths greater than1,700 nm without further chemical intervention. Increasing the indium content used can extend this range up to around 2,600 nm, but with the trade-off of degrading overall performance and increasing the cost by 400-500%.
In contrast, lead sulphide based (PbS) QDs are capable of similar or superior performance at a fraction of the cost of InGaAs technology. With flexible broadband tunability covering visible, near-infrared, SWIR and mid-wave infrared (MWIR) wavelengths; strong optical absorption and large dielectric constants; and compatibility with a wide range of substrates and form factors, PbS QDs are particularly well-suited for SWIR imaging and sensing.
Combined with their lower cost of production, this technology is making SWIR capabilities accessible to a much broader range of businesses.
This low cost is possible thanks to innovative QD formulation techniques that facilitate production at kilogram scale. Modern synthesis methods remove the need to deposit QDs in 14-16 layers and chemically treat or wash each individual stage; a process known as ‘spin coating’. Instead, QD crystals can be deposited in a single layer, eliminating the requirement for further chemical processing and minimizing the otherwise significant risk of defects in the films, such as cracking and inefficient exchange processes.
Processes like this reduce the time and waste involved in QD production and drastically improve the accessible material yield. As a result, high-performance PbS QDs can be produced at a sufficient scale to meet the growing demand for SWIR-sensitive technologies.
Applications
Due to their low cost and high performance, PbS QDs significantly widen the use cases for SWIR imaging in machine vision applications. QD-equipped sensors can be ‘seen’ through sealed containers to monitor fill levels or check for damage and can penetrate silicon to facilitate contact quality checking in semiconductor component fabrications. At certain wavelengths, SWIR light is highly absorbed by water, meaning images with high water content appear black under such conditions. This enables cameras to detect bruised or spoiled fruit, or black ice on the roads, for example.
Notably, other wavelengths such as NIR and MWIR—also commonly used in machine vision—are incapable of performing similar functions.
SWIR sensors also offer improved performance in all light and weather conditions. Whereas other wavelengths are scattered by dust, fog, and precipitation, SWIR light is unaffected, meaning these cameras perform optimally regardless of conditions. This grants them great potential in defence and security, as well as in automotive sensors such as light detection and ranging (LiDAR) systems—extending the effective range of such sensors to 500 m.
QDs also have the potential to benefit other emerging technologies. Growing numbers of manufacturers are integrating AI into their machine vision systems, leveraging its power to improve automation and efficiency. AI offers vision systems a tool for recognizing patterns around them, comparing the images they capture with an evolving database of reference images. For example, using AI, machine vision systems can employ natural language processing to better understand and interpret text on labels. As the technology advances, more exciting applications like deep learning will enable the automation of highly complex processes.
This acceleration in AI’s potential will be aided by QDs enhancing the data it can access. AI works based on analyzing data sets and identifying patterns. This data set is all it knows, meaning its effectiveness is dependent on the quality of that information. QD-equipped sensors, capable of capturing and analyzing vast quantities of ‘invisible’ data, and more accurately perceiving the world around them than existing alternatives, will improve the data AI can access and make these tools significantly more powerful.
This is not to mention the potential of this technology in other sectors. In medicine, QDs are being used to detect hidden conditions beneath a patient’s skin without the need for intrusive surgery. In consumer electronics, SWIR capability could facilitate next generation smartphone spectroscopy, or enhance virtual and augmented reality devices. In photovoltaics, solar cells equipped with QDs can more efficiently generate excitons than silicon or copper indium gallium selenide alternatives, thanks to their high photo stability and tunable band gaps. Using QDs effectively extends the proportion of light that solar cells can convert, from 32-33% to a potential 66%.
Challenges to Overcome
The primary barrier to the mass proliferation of QD technology for machine vision applications is its scalability. Many developers struggle with poor control of nanoparticle synthesis, environmental degradation, and limited batch-to-batch consistency. Overcoming these challenges requires specialized expertise in QD synthesis and scale-up, surface chemistry, ink formulation, fabrication, and testing.
What is more, the inherent toxicity of the best performing QDs has so far restricted their use in mass-market applications. To achieve the highest possible efficiency, QDs must feature coatings made from substances such as cadmium or lead, which are heavily regulated in many markets due to their harmful effects. Although alternative solutions are available that swap heavy metal for substances like Indium, these generally offer lower performance. The best performing lead-free QDs are responsible to wavelengths up to 1,550 nm which, while suitable for certain SWIR sensing applications, restricts them from tasks requiring higher sensitivity.
Lighting the Way
QD technology is not some far-off concept; it is already being utilized today. Several major industry players have already introduced QD-based imaging devices for industrial use as an alternative to their existing InGaAs technology. These devices have demonstrated small global shutter pixels of less than 2,000 nm pixel pitch while offering high performance and significant reductions in production costs.
As QD technology advances and the barriers to scale-up are overcome, these semiconducting nanocrystals will increasingly be used to make SWIR imaging and sensing more cost-effective. In addition, the high tuneability of QDs could also enable them to tap into MWIR wavelengths, offering a cheaper alternative to cameras that often cost 10-100 times the value of SWIR equivalents.
Although QDs are unlikely to replace InGaAs for SWIR sensing in the near term, this technology is ideally positioned to complement it. By making SWIR capabilities more affordable and accessible, QDs are bringing the future of machine vision into reach—and that future looks increasingly bright.
About the Author
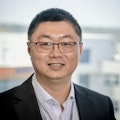
Hao Pang
Hao Pang, PhD, is the founder and CEO of Quantum Science Ltd (Warrington, England, UK). Pang led the initial business fundraising, built the team and global business strategy and developed the technology and IP program. Prior to founding Quantum Science, Pang held a vice president role at a leading LSE-listed technology company, where he led a multi-million USD technology licensing deal, developed the supply chain and successfully introduced the technology into the global electronic markets. Pang has 20 years materials research and commercialization experience and has a PhD in Materials Chemistry from the University of Strathclyde (Glascow, Scotland, UK) and an MBA from Manchester Business School (Manchseter, England, UK).