Augmented reality glasses provide eyes for remote technical support
Contaminants accidentally entering water streams creates immediate, potentially dire problems for the environment and surrounding community. Whether its gas stations whose underground storage tanks have contaminated the local aquifer or hundreds of miles worth of nearby rivers, when such occurrences happen, companies like Encotech (Eighty Four, PA, USA; www.encotech.net) step in to provide environmental remediation systems and services.
Following the installation of such a system, follow up maintenance work may be necessary. Previously, Encotech would book a hotel room for a technician, then fly him or her along with their tools to remote locations often more than 1,000 miles away, where the person would rent a car and drive up to a few hours to a site only to spend 15 minutes making small adjustments, explains Jason Lalli, Director of Business Development, Encotech.
To cut down on the time and costs involved, the company sends camera-equipped wearable augmented reality glasses with all new systems to view exactly what an on-site technician sees to get simple, quick fixes out the door (Figure 1).
“If clients encounter a hurdle in setup or otherwise need to troubleshoot, remote support for the glasses is turned on and the technician starts wearing them around the facility,” says Lalli. “Previous troubleshooting calls took hours on end but having these glasses on hand saves incredible amounts of time.”
To provide this remote support, Encotech uses two pairs of Epson Moverio (Long Beach, CA, USA; www.epson.com) smart glasses, the BT-300 and BT-350 ANSI, the latter of which features an American National Standards Institute (ANSI) Z87.1 safety-glass compliant design for applications where it may be required. Both glasses feature a 5 MPixel camera, Intel (Santa Clara, CA, USA; www.intel.com) Atom x5 1.44 GHz Quad Core CPU, and 30 Hz refresh rate, while offering a 6-hour battery life that varies based on settings and environmental conditions. Additionally, when leveraging the Moverio Assist app and smart glasses, Epson’s Si-OLED display is projected in a wearer’s field of vision into their surroundings and allows field technicians to view instructions, photos, PDFs, and videos while communicating with remote company personnel in real-time (Figure 2).
In a trial with the smart glasses, Lalli was on the phone with a technician trying to describe a situation. For 10 minutes or so, he attempted to explain which valve to adjust, to no avail. Once the technician put the glasses on, Lalli was able to visually guide him to the correct location of the valve and provide simple instructions on how to properly adjust the system, instead of trying to explain the process over the phone.
“With the glasses on, the two of us saw the same thing, which helped get the technician over to the correct location and adjust the valve, in just minutes,” he says. “The time spent trying to explain where to physically go around the system and then what to do versus just being able to watch what he sees, that is phenomenal. A service call like this for us could take 3-4 hours, and with the glasses, it took, in this case, 45 seconds.”
In a real-life deployment, Encotech required an adjustment on an advanced crossflow particulate filter. To configure such a filter properly at every site requires some fine tuning when setting it up the first time due to variable conditions, says Lalli. The adjustment was required for one particular valve, but instead of sending a technician, a pair of glasses were sent to the site and a person with no experience with this type of filter put them on.
“When walking someone through a system they don’t understand, it can be very difficult,” says Lalli. “With the glasses though, it is possible to use someone as eyes and hands to direct him or her to make the necessary adjustments to the system and solve the problem quite easily. The way the company uses it right now provides simple, effective customer support that would otherwise be staggering in the amount of effort we'd have to put in to get such fixes out the door.”
About the Author
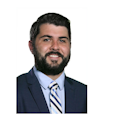
James Carroll
Former VSD Editor James Carroll joined the team 2013. Carroll covered machine vision and imaging from numerous angles, including application stories, industry news, market updates, and new products. In addition to writing and editing articles, Carroll managed the Innovators Awards program and webcasts.