Vision system automatically counts piston rings
To decrease cycle times and lower production costs, IP Rings (Chennai, Tamil Nadu, www.iprings.com), a manufacturer of piston rings for Tier 1 and Tier 2 suppliers to Indian automotive manufacturers, turned to machine vision. The company previously sorted, counted, and packaged piston rings to ensure that each set shipped contains the right number and type required for various types of engines that its customers assemble.
Sorting and counting each batch of rings was time consuming and labor intensive because each batch contains 100 or more rings varying in size from a minimum width of 0.29 mm to a width of up to 0.79 mm. Counting the precise number of rings is critical and helps avoid confusion during piston set assembly, as extra rings or not enough rings requires manually recounting the set.
To automate the counting and sorting process, IP Rings turned to Industrial automation integrator Qualitas Technologies (Bengaluru, Karnataka; www.qualitastech.com) to develop a semi-automated machine that relies on machine vision.
The machine vision system comprises a 5 MPixel camera from Dahua Technology USA (Irvine, CA, USA; https://us.dahuasecurity.com/machine-vision), Teledyne DALSA’s (Waterloo, ON, Canada; www.teledynedalsa.com) Sherlock software running on an industrial PC from Neousys Technology (New Taipei City, Taiwan; www.neousys-tech.com), and a red diffused bar light (438 lux).
During operation, an operator chooses a model name along with the predefined number of rings for a bundle, then loads a batch of rings onto a custom jig and triggers the camera to capture the image of the rings in a 145 mm field of view. Mounted at 45° to avoid ambient lighting effect, the red bar light provides illumination. Two stoppers, one fixed and one movable, hold the rings within the given region-of-interest. The software counts rings by tracking the edges.
“Our main objective was decreasing the cycle time and increasing accuracy by automating the tedious task of counting piston rings,” said Raghava Kashyapa, CEO of Qualitas Technologies “Eliminating ambient light was a major challenge, so we used custom jig and diffused red light to properly illuminate the rings of all sizes and textures.”
The software’s Edge Count tool recognizes slight discrepancies such as larger gaps than expected between the rings and substances on a ring that alter its appearance. For edges that appear absent, the software generates a warning and highlights the problem, allowing the operator to verify the count and adjust the stack to resolve the issue.
Results display in the PC-based software’s custom user interface as pass or fail, with pass batches sent for packing and shipping to the customer. Cloud-based image storage provides operators with access to monitor inspection results and overall performance, allowing the adjustment of parameters as needed.
While manual counting of 100+ rings took more than 5 minutes, the automated machine completes the task in 10 seconds, including the time required to feed the rings to the jig. As a result, IP Rings plans to deploy more jigs to further improve efficiency.
“Our experience with Teledyne DALSA made them an ideal partner for this application,” said Kashyapa. “Sherlock’s vision ensures a high degree of accuracy by recognizing minor variations with the rings that could alter the final counting process.”
Related stories:
Intelligent feeding system combines robot, vision, and flexible feeder into one software environment
Machine vision system measures paint coating thickness on steel products
Deep learning software enhances PCB inspection system
Share your vision-related news by contacting Dennis Scimeca, Associate Editor, Vision Systems Design
SUBSCRIBE TO OUR NEWSLETTERS
About the Author
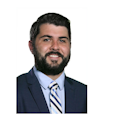
James Carroll
Former VSD Editor James Carroll joined the team 2013. Carroll covered machine vision and imaging from numerous angles, including application stories, industry news, market updates, and new products. In addition to writing and editing articles, Carroll managed the Innovators Awards program and webcasts.