Barcode scanning vision system provides accuracy for warehouse truck loading operations
A pet supply manufacturer saved around 40 hours weekly after making the switch from manual barcode reading with hand scanners to a pallet scanning system that doesn’t require forklift drivers to step down from the vehicle during their shift.
Normerica (Port Credit, ON, Canada; www.normericainc.com) produces cat litter, dog food and treats, and private label products, stored in and shipped from four warehouses in North America. Historically, forklift drivers would use handheld barcode readers to scan 1D linear barcodes on pallets before picking the pallets up with the forklift or just before loading the pallet onto a truck.
According to Simon Than, from warehouse management solution developer Portable Intelligence (Markham, Ontario, CA; www.portable-intelligence.com), error rates recorded in the high single digits for issues like shipping too little or too much product, sending the incorrect products altogether, or pallets not being scanned at all.
At one of the warehouses, 60 trucks could be loaded per day with 26 pallets on each truck. At the same facility, approximately 40 inventory turns—the functional equivalent of shipping every single pallet and then refilling the warehouse—took place annually. Normerica wanted greater shipping speed as well as higher accuracy and potentially faced the need to acquire larger warehouses with more dock doors, hiring more drivers and forklifts, and buying more hand scanners to increase shipping volume.
Portable Intelligence worked with Normerica to install stock management software and shipping label systems at the warehouse. Normerica also wanted also to install a tracking solution to replace the manual pallet scanning system. A radio frequency identification (RFID) tracking system included hardware, set up time, and tag production costs that Normerica didn’t find palatable.
Instead, Portable Intelligence worked with industrial machine vision solution developer Artemis Vision (Denver, CO, USA; www.artemisvision.com) to install the RaPTr (Rapid Pallet Tracker) warehouse scanning system.
The 1D barcodes were replaced with 2D barcodes approximately a month before the RaPTr system installed. While the system does not strictly require the use of 2D barcodes, they provide the best scanning performance, says Andrea Kuenker, Marketing and Design Specialist at Artemis Vision. Because of the high inventory turns, this provided enough time to get most of the inventory in the warehouse changed over to the new 2D barcode system, says Than.
The RaPTr installation at the Normerica warehouse employs two 5 MPixel Basler AG (Ahrensburg, Germany; www.baslerweb.com) acA2440-35um cameras, mounted on the wall next to a loading dock. The cameras connect to an OnLogic (South Burlington, VT, USA; www.onlogic.com) Helix series industrial PC with keyboard interface and hardwired via Ethernet cable into the warehouse’s master control system. Having two cameras provides multiple fields of view and makes it easier for the RaPTr system to read the barcode, especially when the location of the barcode may vary from pallet to pallet.
A 24-in. ViewSonic (Brea, CA, USA: www.viewsonic.com) TD2421 1080p Dual-Point Optical Touch Screen monitor mounts on the wall above the camera. A CMVision (Houston, TX, USA; www.cmvision.co) IRP24-850nm Wide Angle 24pc High Power LED IR Array Illuminator provides lighting for the application.
When an empty truck arrives at the Normerica warehouse, a supervisor assigns its loading dock door to a particular product order using the warehouse’s master control system. This creates the database entry against which the RaPTr system compares barcode scan results.The Basler camera scans the pallet’s barcode when the forklift approaches the loading dock (Figure 1). If the pallet belongs on the truck, a green bar displays on the monitor (Figure 2). If the pallet does not belong on the truck, a red bar appears. Than notes that the message text accompanying the green or red bars is customizable. The highlighted barcode also displays on the monitor, to verify for the driver that the camera can see the barcode clearly.
An alert sounds if a scanned pallet does not belong on the truck at that loading dock. The driver returns the incorrect pallet to the warehouse, and a supervisor clears the error message either via the keyboard connected to the PC at the loading dock or remotely from a terminal at their office desk. If a supervisor does not clear these alerts, the warehouse management software will not print the paperwork the truck driver requires before leaving the warehouse, an option that can be turned on and off in the software configuration.
In addition to scanning the pallet’s barcode, the RaPTr system also captures a timestamped image of every pallet and stores the images in a database. Shipping managers can then review photographic proof if questions arise about a truck’s contents.
Installing the pilot system at a single loading dock in the warehouse took half a day, Than says. It took a full day to adjust the cameras’ focal length, make sure barcodes were captured properly, add infrared lighting, and integrate RaPTr into the warehouse’s master control system.
Ambient lighting posed a challenge as the loading dock doors can admit sunlight that tends to wash out the glossy labels on the barcodes, says Than. This required the addition of IR lighting and a software adjustment to increase white balancing speed when the camera changed focus from the dark warehouse environment to the bright illumination at the loading dock.
Very little personnel training was required, according to Than, to adjust for the installation of the pallet tracking system. Supervisors had to learn how to use the master control system to assign shipping orders to loading docks and forklift drivers had to learn to maintain a “quiet zone” in front of the loading dock, keeping any pallets out of the cameras’ field of view before loading them into the truck.
According to Than, loading time for each truck has been reduced by 25 minutes. Normerica saves eight to nine employee hours daily for no longer having to manually scan each pallet before loading it onto a truck, resulting in higher shipping volume.
RaPTr requires very little system maintenance, adds Than. While Artemis Vision recommends cleaning off the camera lenses at the beginning and end of every shift, cleaning the lenses only once a week suffices (even if the facility ships dusty kitty litter, Than notes).
In addition to loading time efficiency, Than says Normerica also expects to save hundreds of thousands of dollars from reduced compliance fines. He adds that RaPTr has more than paid for itself and the company in the near future intends to install the system at its other three warehouses.
“I also haven’t had to replace a handheld barcode scanner in six months,” says Than. “Now, the system’s fixed in place. It’s not moving around in someone’s holster, on a forklift truck, and it’s not walking around and disappearing.”
“I think there are opportunities to use this system for inventory count,” says Than. “Put it on a cart, wheel it around, and it can pick up all the barcodes from the pallets in the warehouse. That’s an application that could be feasible at some of our facilities. It would be much quicker and much more accurate versus having someone go around with a piece of paper and a pen.”
Inventory transfers present another potential use for the system, says Than. “Put this camera system at an intersection. If a pallet moves from area A in the warehouse to area B, it automatically registers the transfer. Typically that would be at least two scans—scan the barcode, scan the final resting place for the pallet. With this hypothetical automated system, as soon as you cross the threshold from area A to area B the camera picks it up, and the warehouse inventory tracking system updates automatically.”
Than stresses these are not applications Portable Intelligence is currently working on, but opportunities the company may pursue in the future.
About the Author
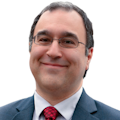
Dennis Scimeca
Dennis Scimeca is a veteran technology journalist with expertise in interactive entertainment and virtual reality. At Vision Systems Design, Dennis covered machine vision and image processing with an eye toward leading-edge technologies and practical applications for making a better world. Currently, he is the senior editor for technology at IndustryWeek, a partner publication to Vision Systems Design.