Next generation inspection robots the focus of European Union’s SPIRIT Project
As part of the European Union’s framework programHorizon 2020, a consortium of partners from science and industry are collaborating on next generation inspection robottechnology.
SPIRIT, according to the group, aims to develop an “inspection skill” for robots that takes the step from programming of complex inspection tasks to configuring such tasks, which will substantially reduce the engineering costs when setting up inspection robots in industrial environments. The main result will be a software framework that consists of two parts, the first of which is the “offline framework,” which hands the model-based automatic coverage planning for complex parts and various image-based inspection processes as well as the automatic robot program generation. This, according to The SPIRIT Project, will include a generic interface that enables the exchange of process models (for different inspection technologies), of the CAD model of the part (for a different type of product to be inspected) or of the work-cell model (for a different kinematic structure).
The generic “inline framework” deals with sensor data mapping to transfer 2D images data to the object model. This, according to the group, will provide the “backbone for the real-time execution of the actual inspection process, including the synchronization of data acquisition and robot motion.”
The three-year SPIRIT research project will develop a system solution that can be equipped with a range of different inspection devices: video cameras for surface inspection, thermal imaging cameras for crack detection, X‐ray sensors or 3D‐sensors to check for completeness. The software being developed enables the robot to perform automatic path planning for each of these different inspection tasks. The system will be fed a CAD model of the component and—to prevent collisions—that of the work cell. It then automatically calculates the path for the robot, depending on the sensor system and inspection task.
As part of the project, InfraTec will provide technology and expertise for thermal imaging inspection. At the Austrian specialty steel manufacturer BÖHLER, a subsidiary of Voestalpine AG, crack detection of forged high‐performance parts for aerospace, energy generation or drive technology will be automated using high‐end thermographic technology from InfraTec, according to InfraTec.
Other users in the project network, according to The SPIRIT Project, are the FIAT Research Center, with automated inspection of engine assemblies, as well as the FACC company, manufacturer of
CFC lightweight components for aviation and the automobile industry, where the goal is greater flexibility in nondestructive inspection of these high‐tech components.
View more information onThe SPIRIT Project.
Share your vision-related news by contactingJames Carroll,Senior Web Editor, Vision Systems Design
To receive news like this in your inbox, click here.
Join ourLinkedIn group | Like us on Facebook | Follow us on Twitter
About the Author
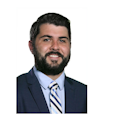
James Carroll
Former VSD Editor James Carroll joined the team 2013. Carroll covered machine vision and imaging from numerous angles, including application stories, industry news, market updates, and new products. In addition to writing and editing articles, Carroll managed the Innovators Awards program and webcasts.