With so many components, systems, and subsystems in cars today, no one wants to worry about the many possible ways it could breakdown and leave you stranded on the side of the road, waiting on AAA, Uber, or Lyft to come to the rescue. Most us aren’t concerned about such things because automotive manufacturers deploy machine vision systems across their production operations to verify proper assembly and ensure reliability.
For example, engine cooling fans prevent loss of engine performance and overheating. However, achieving proper air flow through the radiator to sufficiently cool a car’s engine requires that fan and shroud size precisely match. Automotive technology, systems, and components manufacturer DENSO Manufacturing Michigan (DMMI; Battle Creek, MI, USA; www.denso.com) accomplishes this using black embossed lettering on its glass-packed polyurethane fans.
Formerly, operators manually read the lettering on the fans, matching them to the appropriate shroud. However, this process was error prone and time-consuming due to the low-contrast lettering. To improve the process, DENSO developed a machine vision system capable of performing optical character recognition (OCR) on the embossed character. Making use of computational imaging techniques, the system captures multiple images under different lighting conditions and combines them to enhance difficult-to-see details.
To recognize the lettering on the black embossed parts, a V20-ALL-P3-W-M-M2-L VISOR vision sensor from Sensopart (Wieden Germany; www.sensopart.com/en/) uses Multishot computational imaging technology, which involves the use of four lights and proprietary algorithms that combine multiple images to enhance details that would be difficult to see using standard illumination methods. Four dark field bar lights from Smart Vision Lights (Norton Shores, MI, USA; www.smartvisionlights.com) form a square pattern seven inches above the area where the part is imaged.
“This process required the ability to read these numbers and verify that the correct fan is going onto the correct assembly,” says Jordan Kopp, Automation Team Engineer for DENSO. “To accomplish this, we developed a vision system that performs OCR on the difficult-to-read black molded plastic.”
Following image capture, Sensopart software processes the images and merges them together resulting in an image containing a readable set of part numbers. The OCR tool within the software then reads the characters and confirms whether the part is the correct number.
For image capture, the vision sensor sits 14 inches above the fan/inspection station. This vision sensor features an integrated processor for onboard image processing, 1440 x 1080-pixel CMOS image sensor with 3.45 µm pixel size, integrated lens with 12 mm focal length, and motorized focus.
Fans arrive at the loading station on a pallet and an operator loads them onto a gravity conveyor where they proceed fifteen feet to the inspection station. As parts enter the field of view of the vision sensor, a Banner Engineering (Minneapolis, MN, USA; www.bannerengineering.com) QS20 series proximity sensor triggers the four-quadrant, flashing bar light array as the vision sensor captures images of the stationary part. Parts index through the gravity conveyor via a Karakuri mechanism from SUS America, Inc. (Elk Grove Village, IL, USA; www.susamericainc.com). By locating the fan hub, the vision sensor software sets the search region for the OCR tool, which moves the region part-to-part rather than having a fixed search region of the OCR tool in space. Doing so makes the search more repeatable, says Kopp.
Over Ethernet, vision sensor output to an ArmorBlock Ethernet I/O Module from Allen Bradley (Milwaukee, WI, USA; https://ab.rockwellautomation.com) controls a proprietary DENSO Poka Yoke (error-proofing) system which allows the process to continue if the correct information is scanned or stop the process if the scan was incorrect.
“Because our fans are embossed, it’s almost like a 3D application,” says Kopp. “Multishot technology allows those letters to really come through and raise off the black background for easier visibility.”
An HMI within Denso’s proprietary system allows the operator to see if the part has passed or failed. If it fails, the vision sensor signals the control system to halt the process, inhibiting removal of the part. When a part passes inspection, the operator removes it from line and assembles it to the shroud, where it will hopefully prevent that early morning, broken-down-on-the-side-of-the-road phone call caused by an overheated car engine.
About the Author
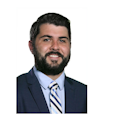
James Carroll
Former VSD Editor James Carroll joined the team 2013. Carroll covered machine vision and imaging from numerous angles, including application stories, industry news, market updates, and new products. In addition to writing and editing articles, Carroll managed the Innovators Awards program and webcasts.