3D camera assists robot in accurate trimming of foam car interior parts
Quality and process management are of great importance to original equipment manufacturers (OEM) and suppliers in the automotive industry, as they strive to ensure high quality, continuously improve the process, reduce waste, and minimize errors.
This is true of all facets of the automotive manufacturing process, including the development of the interior of a passenger car. To ensure perfect comfort in a vehicle, manufacturers utilize foam for armrests and headrests that must be adaptable, flexible, resistant, and durable, while also having a good feel and appearance. Seeking to reduce waste and increase manufacturing effectiveness, Adient (Plymouth, MI, USA; www.adient.com, a leading global manufacturer of car seats and vehicle interior parts, sought the expertise of systems integrator Gips Vision (Marseille, France; http://bit.ly/VSD-GIPS).
At Adient’s plant in Slovenj Gradec, Slovenia, the company’s mechatronic experts worked with Gips Vision to develop and integrate an automated robotic system based on 6-axis robots from ABB (Zurich, Switzerland; www.new.abb.com) designed to trim small foam parts. After a foam part is produced, two robot cells put finishing touches on the product. The first cell involves the robot capturing 3D images of the cell, and the second involves the actual trimming and reworking.
At the first inspection station, a 3D camera identifies an object and the robot moves around the product to create a 3D model, and the exact position of the trim curve on the foam surface is determined, point by point.
In the first cell, an Ensenso N20 3D camera from IDS Imaging Development Systems (IDS; Obersulm, Germany; www.ids-imaging.com) captures a 3D image of the foam. Since the distance and viewing angle of the two CMOS sensors on the camera—as well as the focal length of the optics—are known, Ensenso software can convert these deviations into known lengths by triangulation and thus determine the 3D coordination of the object point for each image pixel and merge them into a 3D point cloud of the foam part to be processed.
The pre-calibrated, GigE camera is built around two 1/1.8” global shutter 1.3 MPixel CMOS sensors, blue LEDs, and an active texture projector system that casts auxiliary structures onto the object to be captured to increase the accuracy of the surface image.
“The camera first identifies the object, then the robot moves the camera around the product, generating a 3D point cloud of the foam headrests or armrests. The result is an exact 360° image of the foam product which the processing unit compares with a given 3D model,” says Thomas Derrien, Innovation Project Leader at Gips Vision.
A 3D point cloud of the foam product is captured with an Ensenso 3D camera from IDS.
Processing is done on an industrial PC in software based on HALCON software from MVTec (Munich, Germany; www.mvtec.com), that also manages the camera.
Reworking begins in the second cell as the robot trims the product using the data acquired in the first robot cell. Guided by the 3D camera, the foam is cut with a grinding tool and during the process any burrs or foam defects that an automobile driver might feel on the surface are removed. The system is reportedly accurate to 2/10 mm and can finish up to 120 pieces of the foam material per hour.
Gips Vision also provides 3D component inspection services for injected foam processes with its Dakota 3D system (www.gipsvision.fr/dakota), installed in several foaming plants worldwide.
About the Author
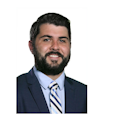
James Carroll
Former VSD Editor James Carroll joined the team 2013. Carroll covered machine vision and imaging from numerous angles, including application stories, industry news, market updates, and new products. In addition to writing and editing articles, Carroll managed the Innovators Awards program and webcasts.