Tire Inspection System Features Multi-Stage AI Pipeline
The giant trucks deployed at construction and mining sites mount off-the-road (OTR) tires designed for use on surfaces like dirt, mud, and gravel. Tire blowouts or fires represent significant expense and/or potential for injury. Visual examinations of OTR tires, therefore, take place at set intervals, requiring trucks to temporarily exit service for inspection.
The Pitcrew.ai system developed by Industrial Monitoring and Control (Carrington, NSW, Australia; www.imcontrol.com.au) captures images and analyzes them for evidence of mechanical issues, generating alerts for site personnel to inform them of any problems without breaking the normal flow of operations.
Pitcrew.ai features a Teledyne FLIR (Wilsonville, OR, USA; www.flir.com) A615 thermal camera, Neousys Technology (New Taipei City, Taiwan; www.neousys-tech.com) Nuvo-7166GC PC, and three 370 W solar panels that charge a 48 V 300 AH LifePO4 battery, all mounted on a skid placed on the side of the road. The system has three versions—mining, compliance, and fleet—differentiated by what the artificial intelligence (AI)-based software looks for in the captured images.
The compliance and fleet versions deploy primarily for brake inspections, according to Tim Snell, Director at Industrial Monitoring and Control, and use identical AI models and datasets. A compliance authority provided images that were matched with roller brake force testing machine data to create the datasets for AI training and testing.
The mining version detects “hot tires,” or tire damage such as rock cut (a cut into the very top layer of the tire) and tread separation (the splitting of the tire layers after the initial cut takes place). In this case, OTR tire crews collected ground truth data with regard to tire separation size and severity to help produce training and testing images. The mining version has a much larger and unique dataset compared to the compliance and fleet versions.
The Pitcrew.ai image analysis process uses a multi-stage pipeline at the edge and on the cloud.
“Breaking a model up into lots of small chunks has big advantages when it comes to maintaining a production system, primarily that it is simpler to tell at what stage a system/model is weakest, and retraining can be very targeted, i.e. rather than having one huge black box that is computationally intensive to retrain,” says Snell.
Compute at the edge includes motion detection to identify objects in front of the camera and bounding box algorithms to classify vehicle types. If the system recognizes a vehicle of interest, for instance a haul truck at a mining site, image frames extract at 50 fps as full 14-bit raw radiometric data.
Compressed data transmits to a cloud server currently provided by Amazon Web Services (Seattle, WA , USA; www.aws.amazon.com) On the cloud, a mask regional convolutional neutral network (RCNN) identifies objects of interest within the video frames, for instance tires. In the mining version, identifying tire centerlines guides tire tread 2D line scan generation. The line scans de-warp in pre-processing before feeding into the machine learning model that detects any tire damage.
“The process of going to a 2D line scan image of the tire treads seems overly complicated at first,” says Snell, “But, this means that the system can deal with very different vehicle paths through the frame of the camera. It is a major benefit because it means we can place a skid just about anywhere, and the vehicles don't need to change their workflow or follow any special route.”
Using radiometric data rather than converting thermal data to greyscale or color versions prior to classification necessitates considerable thermography and quantitative thermal analysis. According to Snell, the competitive advantages warrant the effort.
“This means that we can come back to any of the images in post processing and take a per-pixel temperature measurement, adjusting factors like emissivity, environmental transmission, color palette, temperature scale, etc., after the fact. It makes it a much more powerful diagnostic condition monitoring tool,” says Snell.
Pitcrew.ai can issue inspection results, including alerts for priority concerns, via email or a public cloud-hosted dashboard. A cloud-hosted service provides SMS messaging. Modbus TCP or Ethernet/IP provide PLC/SCADA interface, with data returned from the cloud to the skid and then sent over WiFi or cloud to site via remote IO module.
Industrial Monitoring and Control is currently testing a beta version of the software that can recognize mechanical imbalances by looking for asymmetry between brakes, struts, and drivelines on both sides of a vehicle. Pitcrew.ai is currently installed at mining sites across Australia and at an oil sands project in Canada.
About the Author
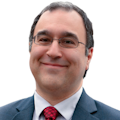
Dennis Scimeca
Dennis Scimeca is a veteran technology journalist with expertise in interactive entertainment and virtual reality. At Vision Systems Design, Dennis covered machine vision and image processing with an eye toward leading-edge technologies and practical applications for making a better world. Currently, he is the senior editor for technology at IndustryWeek, a partner publication to Vision Systems Design.