Vision Systems Tie Logistics/Warehousing Applications Together
If there is one thing we’ve learned from the supply chain crisis, it’s that a lot of organizations don’t know where their things are—especially at earlier and larger levels of the supply chain. Last-mile and fulfillment centers have good visibility. Typically, there are a tracking number and a link in an email sent to a customer. But at the level of pallets, trucks, and shipping containers, there seem to be many more unknowns.
When products showed up on time, no one asked too many questions. Now, supply chain headaches are underscoring the need for reliable traceability and visibility throughout the chain. Under constraints, real-time decision-making becomes more important, but decisions can be undermined by information that gets outdated quickly or simply isn’t available.
Typically, when faced with bottlenecks, one might add labor or build an additional warehouse space. However, widespread labor shortages and lack of warehouse space mean companies must get more productivity from the same space and the same headcount. The alternative is to pay inflated prices to build and hire. When processes break down, change must come.
The shape of that change varies though. Some companies seem focused on automation within the four walls, pouring capital into making fewer, more efficient facilities. However, this puts more pressure on trucking networks to distribute goods farther distances.
Others are optimizing around the trucker shortage, prioritizing smaller facilities closer to the end customer, ideally served by rail to minimize reliance on trucking networks. This means less efficient facilities because the same level of automation across a broader footprint of facilities isn’t affordable. Sometimes these facilities are called micro-fulfillment centers, although nomenclature varies as rail service isn’t often available to the smallest facilities. The advantage of these facilities is delivery speed and minimizing trucker miles.
The nature of the supply chain though is that, well, it’s a chain. Unilateral changes one party makes can’t necessarily speed up or resolve other bottlenecks up or down the chain. Larger systemic bets are also very risky. They take time to play out and can be quite susceptible to market disruptions.
Vision as a Logistics Solution
These trends have led some companies to turn to vision for everything from guiding autonomous vehicles and robots, to reading barcodes, to record keeping. Automated solutions are increasingly attractive for addressing the labor shortages in the logistics sector and speeding up the dangerous or tedious jobs traditionally performed by humans. Both autonomous guided vehicles (AGVs) and autonomous mobile robots (AMRs) embrace multiple imaging components and sensor technologies and require machine vision for path detection. AMRs must go beyond detecting objects in a path and be able to interpret and respond to a dynamic environment. While AMRs and AGVs are currently slower than human forklift drivers and can’t be as flexible, vision aims to close this gap with better 360° imaging solutions as well as better time-of-flight (ToF) based 3D imaging.
Logistics and warehousing tends to run on barcodes. All kinds of information can be encoded ever more efficiently by 2D barcodes, and the more points in place and time they can be scanned, the better the visibility. Although handheld scanners still dominate, companies are beginning to move toward vision-based barcode reading because vision has so many other ancillary benefits. Automated barcode scanning not only addresses challenges with labor shortages and efficiency but when adopted with vision-based scanning, provides pictures of the scans, pallets, and shipping containers for rich opportunities for verification and decision making.
Vision can further be used within logistics to get accurate product dimensions and to detect product in various containers. This kind of technology aids in finding the right packaging for each product, detecting damaged product, flagging when product is missing or unexpected, and optimizing warehouse storage space and truck and shipping container space. Vision and dimensioning also allow automated storage and retrieval systems to detect pallets that will cause jams, increasing uptime and reducing damage.
Related: Machine Vision Lighting Improves Logistics Warehouse Efficiency
Automated packaging equipment has always struggled with packing product without damage and confirming everything left the tote/delivery vehicle and entered the package undamaged. Vision is solving these problems and helping machine builders build more complex automated packaging equipment, because results can be confirmed via camera, so the machine can run faster and fully seal the package for outbound shipping. Without vision, a packaging machine would either have to leave the package open for a person to verify and seal, or a shipper would have to accept costly errors and damage. While order picking remains more difficult to automate, packaging is proving easier and can be enabled by vision, because vision catches the errors that otherwise sink the ROI of automating. As an example, if an automated packaging machine eliminates $500/day of labor but ships seven damaged orders and three incorrect orders, the company quickly loses the savings in labor. Margins are thin, and volumes are high, so if these edge cases aren’t caught, the payback disappears quickly. In more extreme cases, one product breaking in the machinery can damage every subsequent order until someone is made aware of the issue.
When vision systems are networked and report track-and-trace data back to a server, information on a package’s whereabouts, dimensions, contents, condition, etc. can be accessed by multiple users anywhere. With appropriate version control, time stamps, and enough points along the process where imaging can occur, a product can truly be visible from end to end. For most companies, it makes most sense and allows for greatest payback to add vision capabilities and automation incrementally. But as adoption increases, technologies improve, and costs come down, networked vision systems being able to report back many aspects of track-and-trace information become more of a reality.
Logistics and warehousing has historically been a more difficult market for the vision industry to serve because of the speed and flexibility the market requires, as well as the size of the objects (full pallets). Additionally, while a production line may be able to justify a larger capital investment, a forklift or a dock door cannot absorb the same level of capital investment.
But, technological developments are helping. Inexpensive, high resolution, global shutter cameras, for example, allow freezing motion while imaging large items at high levels of detail. Inexpensive off-the-shelf 3D imaging via ToF is also allowing more flexible implementations of 3D.
As a result, vision can now make significant contributions to the logistics market, and investment in vision solutions in warehousing and logistics is surging. The advantages of vision here are many. Vision technology solutions do not require unilateral changes at other levels of the supply chain to realize benefits. Vision provides an extra information layer for datasets that can be turned into predictive paths for problem solving. Vision catches the edge cases that can make automation difficult, create bottlenecks, and require extra resources. Getting rid of these makes companies more efficient and better positioned for future shocks. It also provides the real-time visibility needed to respond quickly and actively manage supply chains. Enhancements with vision, no matter how incremental, make organizations better poised for resiliency over the long run regardless of what future shocks are in store.
About the Author
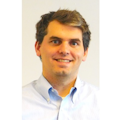
Tom Brennan
Tom Brennan is president and founder of Artemis Vision, which builds machine vision systems for automated quality inspection and optimization for manufacturing and logistics. Brennan is an A3 Advanced Level Certified Vision Professional and is the American Society for Quality's (ASQ) 2021 Hromi Medal recipient for outstanding contribution to the science of inspection and advancement of the inspection profession. He has led the design of many successful machine vision systems for many industries. Brennan got his start in the vision industry designing machine vision vehicle detection algorithms as a research effort for the DARPA Urban Challenge. He holds a BSE in Computer Science from Princeton University.