Line-scan cameras scan freight rail trains
America's Class I freight railroad companies, such as CSX, Union Pacific, BNSF and others operate across the country hauling a broad portfolio of products. To ensure that these products are transported safely, railroads are developing and employing railcar inspection systems that utilize machine vision systems to track and monitor each railcar, conduct inspections, identify problem areas and look for foreign objects that may be present in a scene.
"In recent years" says Scott Carns, Vice President of Operations at Duos Technologies (Jacksonville, FL, USA; www.duostechnologies.com), "railroad companies have realized that efficient monitoring of transportation systems and their related processes could radically streamline their existing operations and increase their current operational process efficiencies."
Tasked with developing such systems, Duos Technologies has developed an integrated system, known as a the rail-car inspection portal (RIP) that can provide 360° images of a train as it moves along a track at speeds of up to 70MPH. Depending on the needs of the customer, the system can be configured in a number of ways. "In its full configuration," says Carns, "under vehicle inspection and side and top car imaging are performed to provide the user with a complete image of the train."
To perform the task of undercarriage inspection, Duos Technologies embedded vision system is placed between the rails of the track (Figure 1). As the train passes over the system, three Spyder 3 2kx1 GigE line-scan cameras from Teledyne DALSA (Waterloo, ON, Canada; www.teledynedalsa.com) fitted with 12mm f2.8 C-mount lenses from Kowa Optical (Torrance, CA, USA; www.kowa-usa.com) image the undercarriage of the car. To obtain a full view of the undercarriage, the center camera is mounted to provide an upward view, while the second two cameras are mounted off-axis to image the sides of the undercarriage.
"Because the train can be moving at different speeds," says Carns, "it is essential that the cameras are properly synchronized and triggered to avoid any distortion effects that would otherwise occur." To accomplish this, five linear contiguous speed sensors of 4ft in length are magnetically attached to the inside of the rail track. As the train passes over these sensors, the sensor's serial output is read by a CPU and used to trigger the cameras.
"Lighting also plays a critical role in capturing high-quality images," says Carns. "This is provided by a specially designed structured lighting system deployed on and around the entire rail that provides the proper amount of lumens to generate high-quality images."
To ensure that the optimum illumination is provided, the angle of these LED lights can be adjusted since they are mounted in a motorized housing moved by stepper motors. "This allows the system to be rapidly installed and then adjusted while minimizing the downtime for the freight company," says Carns.
As with many vision systems that are deployed in harsh conditions, the undercarriage inspection must operate in conditions where dust, snow and rain may occur. To ensure that images can be captured under such conditions, the system employs an air-knife blower that, when required, can blow high-pressure air across the unit to eliminate such foreign particles.
Once images are captured, they are transferred over the cameras' GigE interface to a host PC located yards from the undercarriage imaging system. Here, using proprietary software developed by Duos Technologies, images from the three cameras are stitched together and presented to the user (Figure 2). As well as presenting images of the undercarriage, the system is also capable of detecting features that may be worn or damaged. For example, the presence or absence of bolts mounted on the carrier plate (far right, Figure 2) can be automatically detected and, if any anomalies are found, they are reported to the operator.
While such systems are useful, many freight companies also require the top and sides of each railcar to be inspected. To accomplish this task, Duos Technologies also offers systems that can be used in conjunction with the undercarriage inspection system to provide a 360° view of railcars.
To image the top of the railcar, another Spyder 3 2kx1 GigE line-scan camera is mounted on a gantry approximately 8-25ft above rail track. Similarly, to image both sides of the railcar, two sets of Spyder 3 2kx1 GigE line-scan cameras with 8mm lenses are mounted approximately 15ft from each side of the rail track. This allows the top and sides of the car to be imaged at high-resolution. Captured images are then transferred over the GigE interface to host computers where they are again stitched together and presented to the user (Figure 3).
"Because the user may only wish to view individual cars," says Carns, "the undercarriage imaging system employs a radio frequency identification system from TransCore (Nashville, TN, USA; www.transcore.com) that detects location and time data from the Automation Equipment Inventory (AEI) tags located on each car. Using this data, the system is capable of singulating each rail car and presenting an image of it to the user."
Thus, operators can inspect the entire train by selecting the side of interest and scrolling through the panoramic view. Any faults or anomalies found by the system are marked on the panoramic images and presented to the operator who either acknowledges the suggested detection as valid or rejects the detection as invalid. The operator can expand the event to view car, additional images, enlarge specific areas for a closer view or select areas to enlarge, tag, save, or print.
To allow remote monitoring of the system, Duos Technologies has developed a web-based HMI based on its Centralized Command & Control software, centraco. This software allow multiple users to monitor the status of the system and view the data and images that are captured from remote locations using any commercial browser, eliminating the need to add additional client software and making the system completely distributive.
About the Author
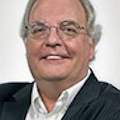
Andy Wilson
Founding Editor
Founding editor of Vision Systems Design. Industry authority and author of thousands of technical articles on image processing, machine vision, and computer science.
B.Sc., Warwick University
Tel: 603-891-9115
Fax: 603-891-9297