Aerial vision system uses high-resolution camera and LIDAR to inspect power lines
Italian aerial data acquisition company Birdview has developed a metric survey system that uses a variety of sensors, including LIDAR, infrared, and CCD sensors in a gimbal mount that can be easily transferred from one aerial vehicle to another.
Birdview’s missions are typically flown in helicopters and are meant to assist utility companies to control and maintain their power and pipeline network and carry out annual quality control checks. Over time, Birdview’s clients requested higher accuracy survey data for their quality control of new and existing power lines and pipelines, so in 2013, Birdview added a Riegl VUX 1 LIDAR and a Phase One iXA-R 160 CCD camera (which is available in North America through 1st Vision) to its vision system.
The iXA-R 160 camera features a 60 megapixel CCD image sensor with a 6 µm pixel size that captures full resolution frames at a speed of 1.3 seconds per frame Their camera is configured with a Rodenstock 40 mm lens and has a USB 3.0 interface, >72 dB dynamic range, and also facilitates bi-directional communication with the flight management system (FMS) and an onboard computer.
The use of the LIDAR in combination with the iXA-R 160 enables the company to obtain higher resolution images needed by clients. These are necessary to capture minute details of the wires’ conductors, poles, and changing swing (changes based on temperature) of the wire in different temperature ranges over the year. The swing of single wires is particularly important to analyze, as this enables utility companies to determine when a cable changes from elastic to static and therefore needs to be replaced.
Helicopters carrying this metric survey system typically operate from an altitude of 150 to 200 meters above the top of power lines, where the LIDAR has a beam footprint of approximately 75 to 100 mm and the iXA-R 160 offers a resolution of two to three cm, which enables an orthophoto to be generated later. The helicopter moves at a slow speed in order to generate the needed number of points per square meter. Standard Birdview projects entail capturing approximately 2,000 to 3,000 images a day.
Phase One’s iXA-R 160 camera was chosen for a number of reasons, including its relatively small size and weight, as the payload of the complete pod needs to be minimized. In addition, the camera can be controlled from the Riegl RiACQUIRE software, which also controls the LIDAR, eliminating the need for another control software to run in the aircraft at the same time. The integration of the camera inside the pod, together with the LIDAR, was done in house.
Alessio Mugnaioli, managing director of Birdview, said: "The colors of the images we get from the Phase One iXA-R camera are outstanding. The images are sharp and clear, but it is especially the color quality that makes this camera a perfect tool for our projects. What makes it so impressive is the fact that the camera can capture this quality even under bad weather conditions. This is important for us as we have to fly long power lines in a short amount of time, especially in places like the Alps, where the weather can change quickly. This helps us to get the job done and produce the highest quality orthophotos for our customers."
The pod itself—which also contains an inertial measurement unit and global navigation satellite system—can be packed up and attached to different aircraft, and returned to Italy for processing. In post-processing, Birdview uses the Riegl RiPROCESS software for the LIDAR data and the software package from TerraSolid for the orthophoto production. Standard deliverables for utility customers include point clouds, shape files, orthophotos, elevation models and 3D models of the powerlines and pipelines. On large power line/pipeline projects, Birdview has found that they are able to achieve on average, an accuracy of about 10 cm.
Alessio Mugnaioli added, "The combination of the Riegl LIDAR and the Phase One camera opened up new markets to us and helped us to grow our business over the last years faster than any time before that."
View more information on Birdview.
View more information on the Phase One camera.
View more information on the RIEGL LIDAR.
Share your vision-related news by contacting James Carroll, Senior Web Editor, Vision Systems Design
To receive news like this in your inbox, click here.
Share your comments, tips, or questions in our comments section below.
Join our LinkedIn group | Like us on Facebook | Follow us on Twitter
About the Author
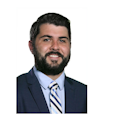
James Carroll
Former VSD Editor James Carroll joined the team 2013. Carroll covered machine vision and imaging from numerous angles, including application stories, industry news, market updates, and new products. In addition to writing and editing articles, Carroll managed the Innovators Awards program and webcasts.