Study Examines iBattery Electrode Foil Inspection Options
Inspection of lithium-ion batteries is not only crucial for guaranteeing performance and quality of the batteries themselves but also for ongoing process optimization. The electrode must be tested at several points during the production process—such as during the creation of the bare metal alloy foil, after coating, and following calendaring—to guarantee the production quality of the finished product.
In this article, we examine the performance of several unsupervised machine learning techniques for finding anomalies in lithium-ion battery electrode foils.
These foils are thin metal foils coated with active materials, forming the anode (usually copper foil) and cathode (usually aluminum foil) of a battery. They are crucial for the electrochemical reactions that enable energy conversion in the battery. The quality of these foils significantly impacts the battery's performance and lifespan.
Difficulties with electrode inspection stem from the web material's fast speed (up to 300 m/min) and the need for a relatively high optical resolution (20 µm/Px) to identify minute flaws. For such challenges, a line scan camera system may be more suitable compared to an area scan camera system.
Some classic image processing algorithms reach their limits when it comes to anomaly detection. This is often the case when the material to be inspected has a strong structure. And many different manifestations of the material can be classified as "normal". The use of deep learning algorithms in quality control is suitable for addressing this problem.
Setting Up The Inspection Study
Different data sets of the battery foils were obtained for this purpose using line scan inspection because slight anomalies on the electrode surface can be found at high production speeds using this technology.
For the study, the following setup was used:
- High-Resolution Image acquisition: Chromasens allPIXA evo 8k CXP line scan cameras, (These cameras, manufactured by the company with whom we are employed, were available for us to use for the study, however, any comparable line scan camera could be used)
- Python-based Image Preprocessing: To pre-process the acquired images, they were cut into patches of size (256, 256, 3) and combined images were created from the images of different illumination geometries. Libraries such as OpenCV were used.
- Dataset Creation for Model Training: To train and test deep learning models, data sets with good and faulty examples are required. Various data sets were generated for this purpose with different lighting geometries for anode and cathode foil.
- Anomaly Detection with Deep Learning algorithms: Machine learning methods such as Autoencoders and other Convolutional Neural Networks (CNNs) combined with different classifiers trained with the acquired images enable identification of defects, such as dust or scratches. The Python libraries TensorFlow and Keras were used for this.
The image data sets needed for additional processing were collected using a conveyor system fitted with an inspection mechanism. Also used were Chromasens Corona II LED line light sources, synchronized with the conveyor speed's camera acquisition line rate via an encoder, and a Chromasens XLC4-1A lighting controller.
Illumination Geometries Used for Inspection Processes
Different illumination geometries—one bright field and two dark field illuminations—were employed to detect irregularities in the electrode foils.
A bright field lighting technique makes reflecting surfaces appear bright since the angle at which the light is incident and the angle at which the camera is aimed are equal. Conversely, dark field illumination involves observing the light that has been dispersed or refracted from the sample. The goal is to find as many flaws on the battery electrode foil as possible by combining these methods.
This inspection system provides the ability to precisely match the strobing frequency of the line light sources with the line rate of each camera. Through this approach every line is recorded three times, but only one light source is turned on for each line of the three cameras. First, the front dark field illumination is activated, followed by a single acquired line with bright field illumination, and finally, another line with the back dark field illumination is recorded. This technique makes it possible to capture the surface in various lighting scenarios. The overlay individual images are then combined into three distinct images using a line shift (deinterlacing), which forms the foundation for further processing steps.
We took images of intact battery electrode foil to serve as the foundation for subsequently creating training sets. To evaluate the image processing pipeline, different anomalies were then added to the data set, including dust, scratches, and moisture. The photos of anomalies were then combined with certain images of undistorted surfaces to create a test dataset. The illustrations below show the influence.
Image Preprocessing
The preprocessing method likewise operates under the premise that flaws are more pronounced in certain lighting conditions. By overlaying images from various illuminations, the goal is to identify a diverse range of anomalies within a single image. This study examines this assumption by comparing a fused dataset of illuminations with datasets from individual illuminations.
Anomaly Detection With Unsupervised Deep Learning Approaches
For anomaly detection, several unsupervised and semi-supervised deep learning techniques were contrasted. Semi-supervised in this context means that only the "normal" error-free data is used to train the neural networks. The normal and abnormal data from the test set is then used to calculate a classification threshold. For this, pre-trained neural networks mixed with various classifiers and reconstruction-based techniques (Autoencoders) were employed. Several experiments were conducted as part of the evaluation process to gauge how well the developed models work. Both the anode and the cathode models were trained and tested with different data sets of the three illumination geometries (dark field front, bright field and dark field rear) as well as with the combined images.
Lastly, a comparison was made between the implemented techniques' inference times on the GPU NVIDIA GeForce RTX 3090. In addition, an investigation was conducted into the impact of dimension reduction of the retrieved features on the inference time and the AUCROC (Area Under the Receiver Operating Characteristic Curve). The AUCROC quantifies a model's ability to differentiate between classes, with values closer to 1.0 indicating a high true positive rate and a low false positive rate across various threshold settings.
In total, 300 normal training images, 200 normal test images, and 200 test images with anomalies (defects) made up the data sets used for research. The size of the anomalies corresponds to an area of roughly 0.5 - 1mm2.
The studies demonstrated that overlaying various illumination geometries was beneficial for the cathode but not for the anode techniques. Dark-field backlighting was the sole technique that produced the best AUCROC values for the anode; an AUCROC of 97% was obtained with a pre-trained model and classifier.
In the data set of the superimposed pictures, an AUCROC of 99% was obtained for the cathode. It should be mentioned, though, that the anomalies evaluated were not produced in an actual production setting. On the GPU NVIDIA GeForce RTX 3090, the inference time (time for one prediction) for a patch with a size of 256 x 256 was approximately 0.12 seconds.
The impact of dimensionality reduction on classification performance was also investigated in an attempt to optimize the inference times. We discovered that while the AUCROC drops, the dimension reduction results in a noticeably faster prediction time. With the data of the superimposed cathode images, for example, inference time of 6 x 10^ -3 s = 6ms with an AUCROC of 90% can be achieved with a dimensional reduction of the extracted features to 4 dimensions.
Summary
This study examined several unsupervised machine learning techniques for finding abnormalities in lithium-ion battery electrode foils. When compared to autoencoder approaches, the pre-trained networks with classifiers approach performed better. We captured several elements of the anomalies of battery foils using various illumination types and geometries, such as bright field and dark field illumination. Overlaying several lighting geometries helped to expose cathode flaws, but it had little effect on the anode, where a single high power dark field illumination produced the best results.
While meeting the real-time requirements in conjunction with the extremely high data rates presents a significant difficulty, the AUCROC values satisfy the necessary inspection requirements. Therefore, to get the best results, machine learning techniques must be integrated with traditional image processing techniques.
The extent to which the deep learning models are optimized for recall/tpr (true positive rate) or max.-f1-score (optimum between precision-recall trade off) depends on the specific requirements of the process since the end-user can determine the follow-up costs and economic effects of the application. Optimizing for recall would be worthwhile if the costs associated with a missed anomaly were very high, even if doing so meant tolerating a greater quantity of false positives (false alarms).
The methods that have been described can also be used for additional surface and foil inspection tasks, such as inspecting the separator foil, coated electrode foil, and bare metal foil.
About the Author
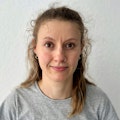
Ines Müller
Ines Müller, M.Sc., earned her master's degree in Applied Information Technology from Lübeck University of Applied Sciences in 2023 while conducting her master's thesis at Chromasens GmbH on automated anomaly detection using machine learning techniques. After completing her studies, she joined Chromasens GmbH as a Vision Application Engineer.