Machine vision’s hottest technologies and most popular applications
We’d like to give you a taste of the results from Vision Systems Design's Solutions in Vision 2021 survey. It is impossible to cover the entire survey in one article. The data-rich results provide information on which technologies may be most worth your time to learn about, what future challenges you may encounter, and what sorts of companies employ machine vision.
Register to view the full survey results
At the end of 2020, we conducted our second annual Solutions in Vision survey, taken by 229 members of the machine vision community: systems integrators, OEMs and machine builders, distributors, research and development experts, end users and manufacturers, and vendors.
We asked how their companies and the industries they serve use five of the hottest technologies in machine vision: 3D imaging, deep learning/AI, embedded, high-speed imaging, and hyperspectral/multispectral/SWIR technologies.
In this article, we cover the level of challenge experienced when our respondents attempt to incorporate these and other machine vision methods into their industries. The full report provides much more. To view it, register here for the full download.
For now, before you register to access the full survey data, here is just a sampling of the results. Thanks to all our respondents for providing Vision Systems Design with a trove of feedback about your experiences and what you would like us to cover as we enter our 25th anniversary year of having the privilege to serve this community.
Seventeen industries and nine applications
Machine vision systems were arguably adopted earliest and most widely by industrial automation. The innovations and solutions produced in this sector will always be a mainstay of Vision System Design’s coverage. However, a breadth of industries together will tell the long-term story of vision system development .
The Solutions in Vision 2021 survey asked respondents to rate on a scale of 1 to 5—1 meaning No challenges encountered and 5 meaning most challenges encountered—how difficult it is for their industries to incorporate nine machine vision technologies:
- High-speed inspection
- Multispectral/hyperspectral imaging
- Defect/flaw detection
- Imaging or Inspecting glossy, reflective, and shiny metal parts
- Random object picking/bin picking
- Random box depalletizing
- Camera mobility
- Vision-guided robotics
- Embedded vision
Into the following industries:
- Aerospace/Military/Defense
- Agriculture/Environment
- Automotive
- Autonomous robotics
- Consumer electronics
- Containers/Packaging
- Drones/Unmanned
- Energy (Oil, Gas, Solar, Wind)
- Food & Beverage
- Forestry/Timber
- General Manufacturing
- Logistics/Warehousing/Distribution
- Medical/Medical Devices
- Pharmaceutical
- Plastics
- Semiconductors/Electronics
- Textiles
Here are the top results for each level of challenge presented by the nine technologies.
High-speed inspection
Interface developments like GigE and GigE10, the CoaXPress 2.0 standard, and faster line scan cameras are some of the innovations that keep high-speed imaging at the forefront of machine vision. For our survey, we asked about the challenge of deploying high-speed imaging specifically for inspection purposes.
According to the results, industries encountering the least challenge for incorporating high-speed inspection, measured by the total of all answers of 1 or 2, are the forestry/timber (63%), drones/unmanned and energy (oil, gas, solar, wind) (62% each), and textile industries (61%).
Top results for industries that experience a moderate challenge, an answer of 3, are the automotive (31%), food and beverage (28%), and aerospace/military/defense and general manufacturing industries (27%).
The industries that experienced the greatest challenge, the total of all answers of a 4 or a 5, are plastics (34%), consumer electronics (33%), and autonomous robotics (29%).
Multispectral/hyperspectral imaging
Multispectral and hyperspectral imaging are two of the hottest topics covered by Vision Systems Design. Their efficacy for agricultural and orbital Earth observation applications feels well-established, with materials analysis also demonstrating the usefulness of this technology. A panoply of applications for imaging outside the visual wavelengths doubtlessly have yet to be discovered.
The textile (60%) and pharmaceutical (48%) industries, with the energy (oil, gas, solar, wind), food and beverage, and plastics industries tying for third place (46%) experienced the least challenge for incorporating multispectral/hyperspectral technologies.
Moderate challenge was reported by the aerospace/military/defense (38%), forestry/timber (37%), and energy (oil, gas, solar, wind) industries (35%). The greatest challenge incorporating multispectral/hyperspectral technologies was reported by the agriculture/environment and semiconductors/electronics applications at 33% each, with consumer electronics reporting 32%.
Defect/flaw detection
If there is an application for which machine vision, in general, and deep learning, in particular, have proven their value, it is the detection of damaged goods or flawed parts. Time and again we see evidence of increased inspection speed and accuracy when machine vision techniques are applied to these tasks.
The industries experiencing the least challenge integrating detect/flaw detection are the textile (59%), drones/unmanned (55%), and containers/packaging industries (52%). Moderate challenge is reported by the energy (oil, gas, solar, wind) (41%), autonomous robotics (39%), and food and beverage industries (38%).
The greatest challenge integrating defect/flaw detection is reported by the medical/medical device (36%), automotive (34%), and pharmaceutical industries (30%).
Imaging or inspecting glossy, reflective, and shiny metal parts
Stable, consistent lighting is integral for a successful vision system. Reflective parts are high on, if not at the top of, the list of objects that can challenge the creation of successful lighting geometry. In some cases, only polarization techniques can account for reflective materials and allow a machine vision inspection system to operate as designed.
According to our respondents, glossy, reflective, and shiny metal part imaging or inspection presents the greatest challenge for the plastics (46%), automotive (43%), and aerospace/military/defense applications (42%). Moderate challenge is reported by the textile (53%) and forestry/timber (42%) industries, with the food and beverage and consumer electronics industries tying for third (34%).
The least challenge employing inspection or imaging of glossy, reflective, and shiny metal parts was reported by the drones/unmanned (54%), logistics/warehousing/distribution (47%), and pharmaceutical industries (44%).
Random object/bin picking
Sorting and pick-and-place applications are often found in industrial automation and logistics, warehousing, and distribution. The technology has evolved from simple picks to deep learning-enabled applications where robots are presented with mixed varieties of objects to sort.
The top three industries reporting the least challenge incorporating random object/bin picking technologies are the textile (53%), drones/unmanned (49%), and plastics industries (48%).
Top results for moderate challenge were reported by the food and beverage (38%), semiconductors/electronics (37%), and pharmaceutical industries (36%).
The industries that experience the greatest challenge deploying random object/bin picking technologies are the automotive (40%) and general manufacturing (36%), with the plastics and autonomous robotics industries tied for third, reporting at 33% each.
Random box depalletizing
Programming a robot to depalletize goods when each pallet is stacked precisely the same way and with the same number of goods is relatively straightforward. This application may require 3D imaging and/or deep learning technologies when the type and position of boxes changes constantly from pallet to pallet.
The greatest level of challenge incorporating random box depalletizing is reported by the consumer electronics (31%), automotive (30%), and drones/unmanned industries (30%). Industries reporting the least challenge were for drones/unmanned and consumer electronics industries at 51% each, textiles at 47%, and containers/packaging at 46%.
Top results for moderate challenge were reported by the energy (oil, gas, solar, wind) (41%), forestry/timber and food and beverage (37% each), and textile, semiconductors/electronics, and aerospace/military/defense industries (35% each).
Camera mobility
Not all camera placements in vision systems are static. Imaging from multiple, different angles can increase fidelity. Camera movement may alter working distance and lighting geometry may have to account for variable camera positions.
The plastics industry reported the greatest challenge incorporating camera mobility at 38%. The containers/packaging industry reported at 34% and the consumer electronics industry reported at 33%.
The automotive (47%), drones/unmanned (43%), and aerospace/military/defense industries (42%) experienced the least challenge incorporating camera mobility. A moderate level of challenge was reported by the textile (47%), general manufacturing (42%), and food and beverage industries (41%).
Vision-guided robots
Vision systems and industrial robots make for a natural pairing. Historically, a robot’s base was fixed or moved very little, with robot arms performing tasks. Now, with more compute available on smaller chips and both robots and cameras decreasing in size, this historic relationship is moving into the realm of mobile robots like those we see deployed for logistics operations in warehouses.
The industries reporting the least challenge incorporating vision-guided robots are the agriculture/environment (54%), textile (53%), and forestry/timber industries (50%). Top results for moderate challenge are reported by the textile (47%) and energy (oil, gas, solar, wind) industries (38%), with the pharmaceutical and containers/packaging industries tying for third place (35% each).
The greatest challenge incorporating vision-guided robotics was reported by the autonomous robotics (37%), automotive (31%), and plastics industries (28%).
Embedded vision
Finally, we come to embedded vision technology. The definition of “embedded” varies, with the common thread being a processor installed into a device that provides compute on or near the device. Board-level cameras, smart cameras, drones, and wearables may all fit into the embedded vision category.
The least level of challenge incorporating embedded technology is reported by the automotive (51%), pharmaceutical (50%), and general manufacturing applications (48%). The greatest level of challenge is reported by the plastics (32%), agriculture/environment (24%), and medical/medical device industries (22%).
Moderate challenge is reported by the agriculture/environment industry at 45%, while the energy (oil, gas, solar, wind) and aerospace/military/defense industries report at 44% each, with the food and beverage and drones/unmanned industries tied for third at 43% each.
Just the tip of the iceberg
We hope you have found this taste of our Solutions in Vision 2021 survey results engaging and elucidating. There is much more data waiting within our full report, that you can register to access here.
Thank you for celebrating with us the 25th anniversary of Vision Systems Design. Plan on enjoying our coverage, and many more informative surveys, for decades to come.
About the Author
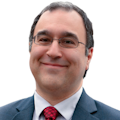
Dennis Scimeca
Dennis Scimeca is a veteran technology journalist with expertise in interactive entertainment and virtual reality. At Vision Systems Design, Dennis covered machine vision and image processing with an eye toward leading-edge technologies and practical applications for making a better world. Currently, he is the senior editor for technology at IndustryWeek, a partner publication to Vision Systems Design.